热压罐成型过程中什么时候使用离型剂
文章来源:未知日期:2020-05-25作者:麦科浏览次数:
航空航天用热固性复合材料制件的生产全过程大体包括八道工序:
(1)准备过程:包括工具和材料的准备。
(2)材料铺贴:包括裁切、铺层和压实。
(3)固化准备:包括模具清洗、坯件装袋以及在某些情况下坯件的转移等。
(4)固化:包括坯件流动压实过程和化学固化反应过程。
(5)检测:包括目测、超声或X射线无损检测。
(6)修整:通过刨机、高速水切割机或铣床修整。
(7)二次成形(该过程不是必须的,但适合用于复杂外形的零件)。
(8)装配:包括测量、垫片、装配。通常采用机械装配,但在一些情况下也采用胶接装配。
热固性复合材料的成形过程通常是相当复杂的。由于精确的成形过程和零件尺寸及零件质量,上述八个步骤中每一步 都有详细的子步骤。成形工序的复杂程度依赖于零件的复杂程度和成形工艺的精确程度,最多可达200多步。其中在第3,4步和第7步工序中使用热压罐,在某些情形下第(8)步也使用热压罐。
下面就具体描述这些步骤。
第1步,准备过程。主要包括工具的准备和材料的准备,其中材料的准备包括主要材料和辅助材料(脱模剂)的准备,数量、有效期以及各自的使用条件等。
第2步,材料铺贴。包括裁切、铺层和压实。该过程将主要原材料按照设计要求以不同尺寸和铺层方式裁减,可以使用样板,也可以使用自动切割机。如将不同的铺层尺寸输入到计算机中,通过图形分析软件(如AutoCAD等和切割机及其相应的软件(如GERBER的Cut-Works软件)将预浸料裁成相应的尺寸,再按照设计的铺层方式进行铺层,最后进行预压实处理。
裁减后的铺层工序能通过许多途径完成,包括手工铺层、自动丝束铺放、自动铺带及纤维缠绕等,也可能包括一个成形工艺步骤 ,例如隔膜成形。近年来,热压罐成形过程的许多工序都有很大进步,但许多航空复合材料零件还是通过手工铺层制造实现的。这是由于手工铺叠大的制件具有更大的灵活性,同时采用自动化设备生产小批量产品的经济性差。手工铺层可以制造几乎任何外形的复合材料制件。
第3步,固化准备过程。它包括制件装袋、辅助材料的裁切、铺放等。在某些特殊情况下铺层和固化为不同的模具,因此该操作也包括从铺贴模具将完成铺贴的制件转移到固化模具中。通常固化准备工放等。在某些特殊情况下铺层和固化为不同的模具,因此该操作也包括从铺贴模具将完成铺贴的制件转移到固化模具中。通常固化准备工作包括制件、模具、脱模剂、真空袋和辅助材料的准备。其中,必须使用的辅助材料包括离型剂、透气材料(用以均匀地分散真空袋体系内的真空)等。
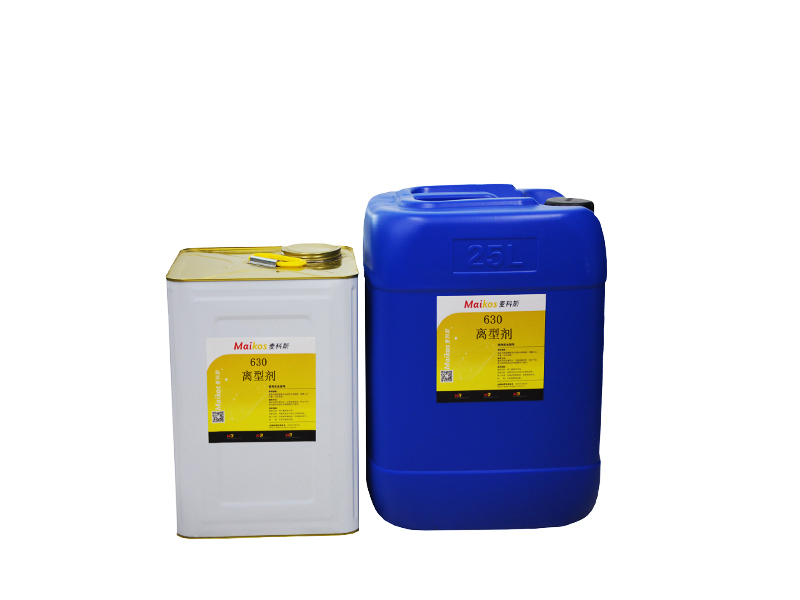
第4步,固化是复合材料生产的必经步骤,包括加热、压实和固化。热固性树脂在-定的固化工艺条件下进行反应,最后形成三维网状结构的结构。对于热固性复合材料,这一步是不可逆的,因此热固性复合材料一旦固化,由铺层或固化过程本身弓|起的缺陷就不可改变地固定下来。由于工业化热压罐相当大,可同时批量加工许多零件,然而这种"批量” 在体现热压罐高效率使用的同时,也给如何严格控制工艺参数提出了严格的挑战。
第5步,检测:包括目测、超声或X射线无损检测。将固化后的复合材料进行质量检测,首先,目测外表,可以观察到未浸润的干斑、缺胶和集胶等外观缺陷,而内部质量检验的通常方法是无损检测法(NDT).主要是用超声C-扫描法,根据超声波声信号的衰减程度可以检测到复合材料内部的缺陷,一般主要指密集空隙和分层。而使用X射线法检测,可以根据不同的增强材料的密度,来显示不同的增强材料的存在形态。例如,为了检测仔热压罐成形过程中纤维的压缩变化或移动,可以观察示踪丝(相对于增强材料来讲,一种密度较大、经X射线无损检测其亮色较亮的纤维的像来预测纤维的压缩变化或移动。
第6步,修整:通过刨光机、高速水切割机或铣床修整。对于固化后的复合材料可能有一定的飞K边或毛刺等,可以通过刨光机或铣床进行修整,以达到设计的要求。
第7步,某些复合材料制件需要进行热压罐二次成形,进行共胶接或共固化,最后制备具有复杂形状的复合材料制件。
第8步,如果采用热固性胶粘剂的固化或层间热塑性胶粘剂的熔融和固结I艺进行复合材料制件的装配,则也需要进行热压罐二次成形。胶接装配工艺很大程度增加了热压罐的负荷,导致很多复合材料制件的热压罐成形过程要经历两倍于常规工艺周期的加热和冷却时间。为提高热:压罐成形的效率, 这类复合材料制件的成形应尽可能采用共固化工艺。共固化工艺能一次固化成形一个完整的复合材料结构件,这种工艺同时需要复杂的固化模具,但它消除了垫片和装配。
(1)准备过程:包括工具和材料的准备。
(2)材料铺贴:包括裁切、铺层和压实。
(3)固化准备:包括模具清洗、坯件装袋以及在某些情况下坯件的转移等。
(4)固化:包括坯件流动压实过程和化学固化反应过程。
(5)检测:包括目测、超声或X射线无损检测。
(6)修整:通过刨机、高速水切割机或铣床修整。
(7)二次成形(该过程不是必须的,但适合用于复杂外形的零件)。
(8)装配:包括测量、垫片、装配。通常采用机械装配,但在一些情况下也采用胶接装配。
热固性复合材料的成形过程通常是相当复杂的。由于精确的成形过程和零件尺寸及零件质量,上述八个步骤中每一步 都有详细的子步骤。成形工序的复杂程度依赖于零件的复杂程度和成形工艺的精确程度,最多可达200多步。其中在第3,4步和第7步工序中使用热压罐,在某些情形下第(8)步也使用热压罐。
下面就具体描述这些步骤。
第1步,准备过程。主要包括工具的准备和材料的准备,其中材料的准备包括主要材料和辅助材料(脱模剂)的准备,数量、有效期以及各自的使用条件等。
第2步,材料铺贴。包括裁切、铺层和压实。该过程将主要原材料按照设计要求以不同尺寸和铺层方式裁减,可以使用样板,也可以使用自动切割机。如将不同的铺层尺寸输入到计算机中,通过图形分析软件(如AutoCAD等和切割机及其相应的软件(如GERBER的Cut-Works软件)将预浸料裁成相应的尺寸,再按照设计的铺层方式进行铺层,最后进行预压实处理。
裁减后的铺层工序能通过许多途径完成,包括手工铺层、自动丝束铺放、自动铺带及纤维缠绕等,也可能包括一个成形工艺步骤 ,例如隔膜成形。近年来,热压罐成形过程的许多工序都有很大进步,但许多航空复合材料零件还是通过手工铺层制造实现的。这是由于手工铺叠大的制件具有更大的灵活性,同时采用自动化设备生产小批量产品的经济性差。手工铺层可以制造几乎任何外形的复合材料制件。
第3步,固化准备过程。它包括制件装袋、辅助材料的裁切、铺放等。在某些特殊情况下铺层和固化为不同的模具,因此该操作也包括从铺贴模具将完成铺贴的制件转移到固化模具中。通常固化准备工放等。在某些特殊情况下铺层和固化为不同的模具,因此该操作也包括从铺贴模具将完成铺贴的制件转移到固化模具中。通常固化准备工作包括制件、模具、脱模剂、真空袋和辅助材料的准备。其中,必须使用的辅助材料包括离型剂、透气材料(用以均匀地分散真空袋体系内的真空)等。
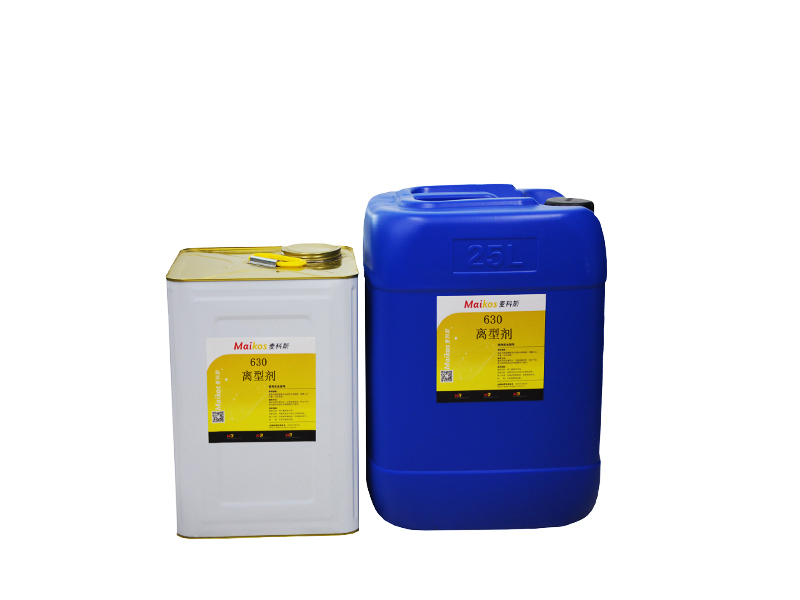
第4步,固化是复合材料生产的必经步骤,包括加热、压实和固化。热固性树脂在-定的固化工艺条件下进行反应,最后形成三维网状结构的结构。对于热固性复合材料,这一步是不可逆的,因此热固性复合材料一旦固化,由铺层或固化过程本身弓|起的缺陷就不可改变地固定下来。由于工业化热压罐相当大,可同时批量加工许多零件,然而这种"批量” 在体现热压罐高效率使用的同时,也给如何严格控制工艺参数提出了严格的挑战。
第5步,检测:包括目测、超声或X射线无损检测。将固化后的复合材料进行质量检测,首先,目测外表,可以观察到未浸润的干斑、缺胶和集胶等外观缺陷,而内部质量检验的通常方法是无损检测法(NDT).主要是用超声C-扫描法,根据超声波声信号的衰减程度可以检测到复合材料内部的缺陷,一般主要指密集空隙和分层。而使用X射线法检测,可以根据不同的增强材料的密度,来显示不同的增强材料的存在形态。例如,为了检测仔热压罐成形过程中纤维的压缩变化或移动,可以观察示踪丝(相对于增强材料来讲,一种密度较大、经X射线无损检测其亮色较亮的纤维的像来预测纤维的压缩变化或移动。
第6步,修整:通过刨光机、高速水切割机或铣床修整。对于固化后的复合材料可能有一定的飞K边或毛刺等,可以通过刨光机或铣床进行修整,以达到设计的要求。
第7步,某些复合材料制件需要进行热压罐二次成形,进行共胶接或共固化,最后制备具有复杂形状的复合材料制件。
第8步,如果采用热固性胶粘剂的固化或层间热塑性胶粘剂的熔融和固结I艺进行复合材料制件的装配,则也需要进行热压罐二次成形。胶接装配工艺很大程度增加了热压罐的负荷,导致很多复合材料制件的热压罐成形过程要经历两倍于常规工艺周期的加热和冷却时间。为提高热:压罐成形的效率, 这类复合材料制件的成形应尽可能采用共固化工艺。共固化工艺能一次固化成形一个完整的复合材料结构件,这种工艺同时需要复杂的固化模具,但它消除了垫片和装配。
下一篇:麦科斯离型剂使用方法及注意事项
分享到:
相关推荐 /Related to recommend
查看更多 >>