为什么碳纤维车架脱模用离型剂而不用脱模蜡?
文章来源:未知日期:2019-11-04作者:麦科浏览次数:
碳纤维车架成型工艺比较精密,很多厂家由于成本原因,使用脱模蜡代替离型剂,结果造成了产品难脱模,损伤了模具。这就是典型的因小十大。麦科斯为大家简单说一下碳纤维车架成型过程以及离型剂的重要性。
1、使用5000到12000根碳纤维原丝,每根只有5至7微米细,它们合成一个丝束,就是我们所说的碳纱。品质越高,碳纤原丝越细。
2、将碳纱编织在一起并与树脂混合,形成预浸碳布,它混合35%的树脂和65%的碳纤维。
预浸碳布都是单向的,因此所有碳纤维都是排列成一个方向。碳布依据车架设计被精确切割以减少浪费。
3、在模具表面涂抹离型剂,新模具最好涂抹2-3遍。
4、使用EPS内模处理并覆盖乳胶,除了气嘴(在后叉的顶部)被完全密封。以前成型用的是气袋,存在碳布折叠,内部粗糙等问题。使用离型剂可以得到很光滑的内表面,而且弯角处也不会出现折叠和无法压实的问题。
5、将预浸碳布围绕在EPS上预成型,需要覆盖5-6层碳布,通过变化角度来增加强度和刚性,一个车架要使用数百片碳布。
6、当所有碳布都贴上去,将预成型的车架放到钢模具中,加热到130°C,使用12bar气压进行加压,维持40分钟,固化成碳纤维车架。
7、使用了离型剂的碳纤维成品,很容易就从模具上分离。这个步骤是把EPS/乳胶从碳纤部件中抽出来,留下光滑的内表面没有任何波纹,一些关键部位的公差需要通过机器打磨实现。
8、一般车架的前三角,后叉是分开成型的,接合部分在预成型时就留有公母阶,它们能无缝的连接在一起,通过胶水并包裹碳纱固定成型。
9、通过品质测试,进行表面处理,喷漆,经过24小时,车架准备好送去装配。
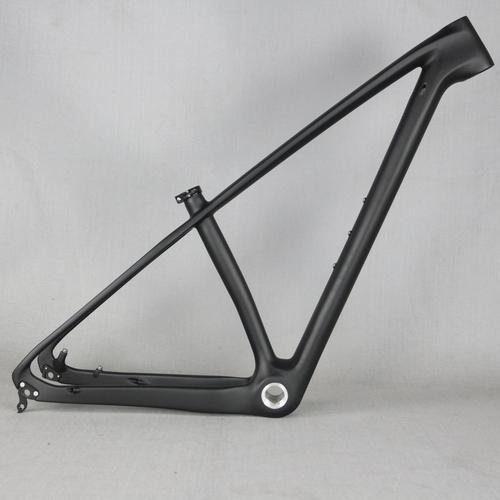
1、使用5000到12000根碳纤维原丝,每根只有5至7微米细,它们合成一个丝束,就是我们所说的碳纱。品质越高,碳纤原丝越细。
2、将碳纱编织在一起并与树脂混合,形成预浸碳布,它混合35%的树脂和65%的碳纤维。
预浸碳布都是单向的,因此所有碳纤维都是排列成一个方向。碳布依据车架设计被精确切割以减少浪费。
3、在模具表面涂抹离型剂,新模具最好涂抹2-3遍。
4、使用EPS内模处理并覆盖乳胶,除了气嘴(在后叉的顶部)被完全密封。以前成型用的是气袋,存在碳布折叠,内部粗糙等问题。使用离型剂可以得到很光滑的内表面,而且弯角处也不会出现折叠和无法压实的问题。
5、将预浸碳布围绕在EPS上预成型,需要覆盖5-6层碳布,通过变化角度来增加强度和刚性,一个车架要使用数百片碳布。
6、当所有碳布都贴上去,将预成型的车架放到钢模具中,加热到130°C,使用12bar气压进行加压,维持40分钟,固化成碳纤维车架。
7、使用了离型剂的碳纤维成品,很容易就从模具上分离。这个步骤是把EPS/乳胶从碳纤部件中抽出来,留下光滑的内表面没有任何波纹,一些关键部位的公差需要通过机器打磨实现。
8、一般车架的前三角,后叉是分开成型的,接合部分在预成型时就留有公母阶,它们能无缝的连接在一起,通过胶水并包裹碳纱固定成型。
9、通过品质测试,进行表面处理,喷漆,经过24小时,车架准备好送去装配。
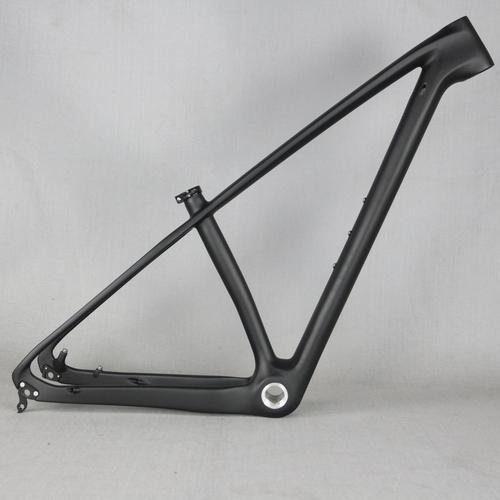
上一篇:选择离型剂要考虑哪些因素
分享到:
相关推荐 /Related to recommend
查看更多 >>